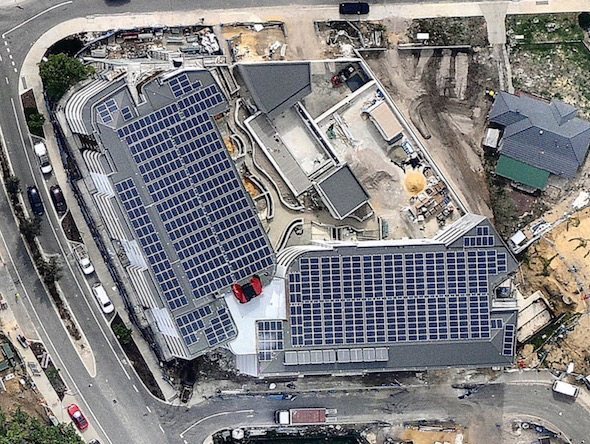
It is an oft-quoted fact that there are over 1.5 million photovoltaic systems installed on Australian roofs. This number is impressive indeed, particularly as in 2009 it was 5 per cent of this amount.
There is, however, a neglected addendum: that these 1.5 million installations are heavily concentrated in one particular segment of our building stock: single occupancy, residential houses that are owned by their occupants.
Solar installations on apartment blocks, for example, are virtually unheard of – and yet these make up the largest and most rapidly growing sector in our cities.
The Solar + Storage project at Sydney’s Stucco Co-operative is beginning to change this. With the support of an Environmental Performance Innovation Grant from the City of Sydney the housing co-op is reinventing itself (or at least it’s electric identity).
What was a typical apartment block, where each unit individually bought electricity from the grid, is becoming a embedded network, where the co-op’s solar with storage system supplies 80 per cent of the electricity.
The co-op sells the solar electricity to the tenants under the terms of a PPA, resolving the split incentive problem with income for the co-op and savings for the tenants. Sharing a single grid connection provides considerable savings in connection charges.
As reported in RenewEconomy, Stucco Co-operative recently concluded an extensive procurement process, commissioning Solaray to install 30.2 kW of Trina solar panels with Enphase microinverters and 43.2 kWh of Enphase AC battery storage.
As one of the project managers I can genuinely say that we are delighted with the commissioned system! Simultaneously, we were astonished to discover how many learning curves occurred on the road to this milestone.
The remainder of this article is dedicated to some of the lessons that arose during the procurement process of the storage system.
Integration – the technical crux
Today’s energy storage devices are far removed from the double A batteries which so often epitomize them. They are complex devices composed of battery cells, inverter(s), a battery management system, and in many cases an energy management system. These, in turn, store the energy, transform the electricity from DC into AC (used in existing circuits), manage the battery’s state of charge and the communications with the inverter, and optimise the use of the battery across time periods ranging from minutes to days.
Each of these components is a specialised piece of kit, and so most of the products in the market today incorporate pieces from multiple manufacturers. The problem with this is that it leaves ample room for miscommunication; both at a hardware-software level and at a company responsibility level. With the Enphase system however, there is one company who is consistently and directly accountable.
Warranties and standards
“Not worth the paper it’s written on,” was one advisor’s response to reading a (well known) battery manufacturers warranty – and this was not the exception. The company’s response, claiming that hundreds of customers were accepting these terms, is anything but reassuring.
Things to look out for in particular include: temperature ratings; the definition of (or ambiguity around) a battery cycle; the effective value depreciation rate; and being tied into in-kind replacements. While the Enphase warranty was better than the rest, it still strongly favours the manufacturer over the customer.
The general absence of standards in the storage industry makes consumer decisions difficult, even for engaged early adopters. A wish list would include: definitions of a cycle, details of lifetime performance, terms of warranties, installation practices, and the conditions of grid connection.
Real risks, outdated rules
The great energy densities packed into modern Lithium ion batteries carry the potential for substantial fires/explosions, which only increases if water is added. We chose Lithium-Iron Phosphate (LiFePO4) batteries because of their reduced volatility (and long term performance), but the basic risk remains. This risk appears to be glossed over in the consumer market.
That these batteries are being installed without registration with a government agency or even mandatory notification to the fire department (and without installation standards) is concern for both consumers and the industry, who are vulnerable to experiencing a fall out.
Meanwhile, the regulations that do exist, are outdated. The Building Code of Australia requires that any battery larger than an electric bike (24V 10Ah – approximately 0.25 kWh) be fully enclosed in a fire proof casing, which would inhibit ventilation and cooling. Gaining approving for an alternative fire solution requires expensive consultant reports and lengthy development consent.
The failure of these rules to distinguish between battery chemistries significantly handicaps non-flammable batteries such as flow batteries and salt water batteries (which are even pH-neutral). A battery option that avoided the dramas and expenses around fire safety would have been very attractive to us.
Many of these issues are understandable in the early stages of the behind the meter energy storage industry.
Indeed, it is often said that the storage industry is where the solar industry was 15 years ago. There is, however, an important distinction: while the solar industry, and the associated regulations, matured over many years – indications suggest that the storage industry is set to explode. Fingers crossed this is purely metaphorical.
Meanwhile back at Stucco; we are still waiting on a few more approvals before installation can begin. Our progress can be followed at www.facebook.com/stuccosolarstorage