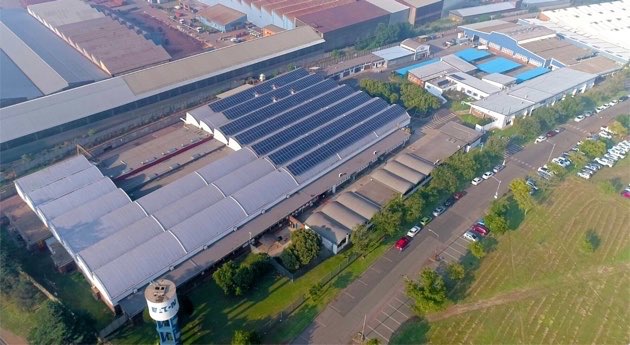
An Eaton production facility in Wadeville, South Africa is reducing its energy and operational costs beyond its expectations thanks to a microgrid that uses first and second life electric vehicle batteries.
The microgrid is reducing the production facility’s monthly utility bill by 40%. Improved manufacturing plant up-time and reductions in diesel-fuel consumption have resulted in operational savings of 56.5% since the microgrid was brought online in March 2018.
“Originally, we anticipated that the payback period would be about five years, including the cost of replacing the energy storage system. However, due to the increase in load-shedding in South Africa, the payback period has decreased significantly,” said John Vernacchia, segment manager, renewable energy solutions at Eaton, a power management company, whose products include microgrid energy systems.
Capable of operating autonomously in the event of grid outages, the Wadeville microgrid includes 232kW of solar PV coupled with 200kWh of energy storage and a power conversion system (PCS). The project makes use of both first- and second life Nissan Leaf electric vehicle batteries for energy storage capacity.

The Wadeville microgrid’s primary value streams
Eaton manufactures low-voltage control and power distribution assemblies at its facility in Wadeville.
“Like elsewhere around the world, the electric grid is aging and our facility had experienced increased load-shedding due to cable faults and scheduled maintenance,” Vernacchia said.
Faced with rising electricity costs and manufacturing downtime due to grid outages and rationing, Eaton’s regional management team at Wadeville began developing ways to resolve these challenges by controlling energy costs, enabling energy independence and improving sustainability.
“Eaton has provided customised microgrids for customers around the world that are able to optimise where, when and how electricity is consumed. The regional facility recognised the potential for improved productivity and reduced costs through this technology,” Vernacchia said.
Eaton’s Wadeville microgrid project addresses the challenge of maximising manufacturing plant productivity and three strategic company goals: energy affordability, sustainability and reliability by delivering four primary value streams, Vernacchia explained:
- Outage avoidance, eliminating production losses due to power outages
- Offsetting energy costs through solar PV and energy storage that relieve pressure on the regional electricity grid, power infrastructure in the area and increase usage of renewable energy
- Peak shaving, which reduces maximum demand charges
- Energy arbitrage, reducing energy consumption from the utility when costs are highest.
“First, the project at Eaton’s South Africa manufacturing site enables peak energy shaving, which reduces our maximum demand charge. It incorporates and maximizes solar PV, which is the cheapest source of energy per kilowatt hour,” Vernacchia said.
“Further, the microgrid is able to island from the utility grid, so that when there is an outage, our manufacturing production is not affected. The project shows how Eaton’s customised microgrid approach uses electricity with greater efficiency and builds dependable power.”
Use of first- and second life electric vehicle batteries
Eaton sees opportunities for similar microgrid platforms to deliver the same value streams elsewhere. “These value streams are applicable in other parts of Africa as well as Asia-Pacific, Europe and the Americas,” Vernacchia said. “It’s more a function of grid coverage, grid stability, and utility rate structures than geography.”
Eaton’s PCS technology is a key to the energy savings and improved quality of service at Wadeville. The PCS “eliminates the need to switch on the 400-kVA diesel gen-set by automatically shifting loads in 2 milliseconds and providing a seamless transfer of power,” Vernacchia said.
In addition, the PCS can operate as an inverter, as well as provide voltage reference for the solar PV system in the case of a utility outage, a critical aspect of the microgrid’s island-mode operations when the utility grid goes down, Vernacchia added.
Eaton broke ground on the Wadeville microgrid project in April 2017. The electric vehicle batteries were shipped by sea to South Africa.
Eaton has a partnership with Nissan to supply both first and second life electric vehicle batteries for the microgrid.
“Since these are designed to go into a car, they are incredibly robust cells. [They] reduce thermal runaway and have less need for cooling, which makes them well suited for Africa,” Vernacchia said.
“Through our collaboration, we have access to both the second-life batteries, which have smaller capex cost, and Nissan’s first-life batteries, which provide the best value.”
A learning laboratory
The Wadeville microgrid serves as a learning laboratory internally and externally, Vernacchia continued. He pointed out that the World Bank Group Enterprise Surveys estimates that manufacturing firms in Africa lose anywhere from 6-20 per cent of sales revenue due to power outages.
Microgrids such as those at the Wadeville manufacturing facility can help companies improve productivity and profits in South Africa and across the continent, according to Vernacchia.
“We actively host microgrid tours and share data to increase knowledge of microgrid technology and share the business case for microgrid development, using the Wadeville microgrid as a case study,” he said.
Eaton has hosted hundreds of individuals, including delegations from commercial and industrial equipment manufacturers facing similar challenges to those Eaton faces in Wadeville since the commissioning of the microgrid, Vernacchia added.
This article was originally published by Microgrid Knowledge. Reproduced here with permission.