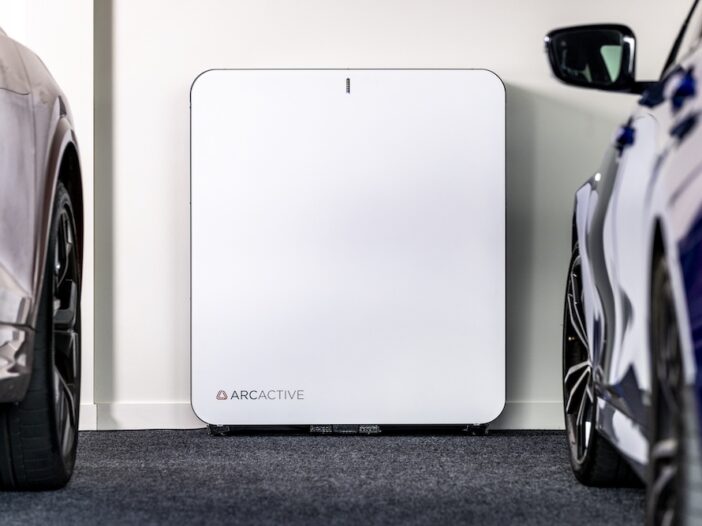
A New Zealand company has unveiled plans to be manufacturing its new-look lead acid home battery energy storage systems in Australia – and selling them for half the price of a Tesla Powerwall – by October 2026.
The timeline and pricing look very ambitious, but the company’s CEO says they can make it work.
The company is Christchurch-based ArcActive and has a $65 million capital raising underway to commercialise its reinvention of the lead acid battery, with plans for a 600MWh factory in either Queensland or Victoria.
CEO Stuart McKenzie expects the $30 million factory to take 12 months to kit out followed by a “generous” six month testing period, which suggests a deal on location is imminent – a prospect he declined to comment on.
The future factory is intended to produce 30,000 units of the company’s 20 kWh battery packs a year, at a price of $4900 for the parts or $7000 installed.
The current going rate for a Tesla Powerwall 2 in Australia, fully installed, ranges between around $13,000 to $15,000.
McKenzie says they’ll be able to charge so much less because the raw materials in a lead acid battery are so much cheaper than those in a lithium ion battery.
“Batteries are mostly a materials cost game and lead is cheap, is the bottom line,” he told RenewEconomy.
“Especially once you get into recycling, I can’t see how anyone could beat the lead acid cost structure.”
At the time of writing lithium was selling for 111,500 Chinese yuan ($A24,454) whereas lead was trading for $US2,144 ($A3,340).
The company also claims its batteries have “infinite recyclability.” The lead, plastic and sulphuric acid can all be used again but the glass fabric separators that stand between the positive and negative electrodes can’t.
The potential to not have to buy lead on market is alluring to ArcActive, with McKenzie saying handling their own recycling is perhaps a decade away.
The tech
ArcActive has tinkered with the lead acid battery to make it more energy dense and smaller, and fixes a hydrogen off-gassing problem common to lead acid batteries.
The starting point is a layered carbon fibre fabric that is combined with a lead paste for the negative electrode, rather than using the traditional lead grid with the paste.
The 50 micron fibre provides extra strength to allow the battery to be compressed together in a new way – more on that shortly – and controls the size of the pores within the battery which stops it from drying out.
A problem with lead acid batteries is that as the electrolyte of sulphuric acid and water heats up, the water can burn off – this is a source of hydrogen off-gassing. Once the glass-wool electrode separator is 80 per cent dry, the battery is “bung”, McKenzie says.
The carbon fibre layers control those pores and keep the separator hydrated, he says.
The second innovation is around bipolarisation and compression.
Compression – mechanically squashing the whole unit together – increases the life-cycle of a lead acid battery but the amount depends on the strength of the materials inside.
Conventional batteries can only be compressed using pressure of up to 30 kilopascals (kPa). But using a layered, bipolar approach with a stronger negative electrode material through the carbon fibre mesh means ArcActive can achieve 100 kPa, McKenzie says.
The bipolar approach is a technique that means one electrode is the cathode and anode at the same time removes some extra materials, and in ArcActive’s battery are layered “like pizza boxes”.
The ArcActive battery itself has been tested in the lab to 4000 cycles at its 15 kWh limit for daily charging and discharging, and 2500 cycles for complete discharging of the full 20 kWh unit.